What is warehousing management? Benefits, systems & tips
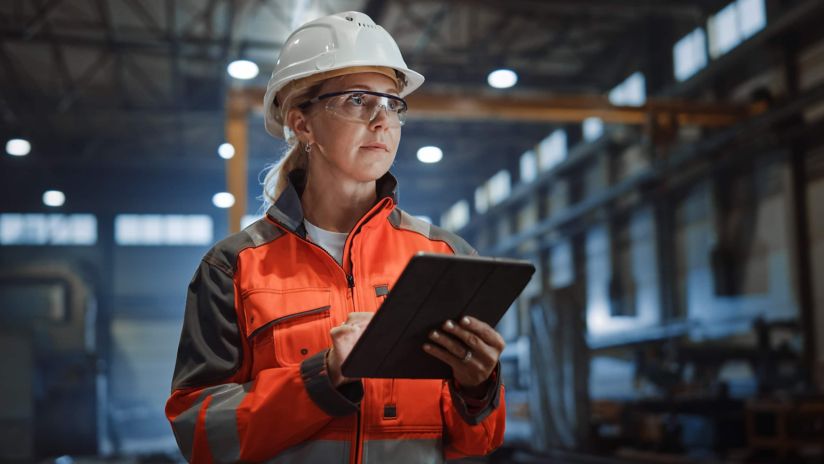
What is warehousing?
First, let’s discuss the meaning of warehousing. To put it simply, warehousing is the process of storing goods.
This means having a space where you can keep your products until you need to distribute them to customers. Your warehouse can be a dedicated section of your existing premises. Or you can engage a warehousing business that provides an external storage facility. This can depend on the size and nature of your business. This form of business operations is very different to dropshipping.
What is dropshipping?
Dropshipping is a retail fulfilment method where the business doesn't warehouse the products it sells. Instead, when a business sells a product, it purchases the item from a third-party and has it shipped directly to the customer. In other words, the business acts as the middleman.
Generally speaking, when dropshipping, business don’t physically handle or stock the products they sell.
What is warehousing management?
Warehousing management goes beyond storing goods. It encompasses the systems and processes you put in place to help oversee your warehouse.
Warehouse management can empower you to achieve desired business outcomes. It can include taking action to help you:
- Optimise business operations
- Aim to reduce costs
- Strive to improve customer experience.
The benefits of warehouse management
Warehouse operations are the invisible backbone. They help ensure your orders get delivered on time. Good warehouse management is all about efficiency - utilising space, helping staff find items, having proper staffing, fulfilling orders smoothly and coordinating with suppliers and shippers. When done well, it can allow for faster product fulfilment. And can help create cost efficiencies. This operational excellence can positively impact relationships across the entire supply chain.
However, optimising all the complex elements of a warehouse isn't always straightforward. That's why many businesses turn to warehouse management systems for assistance in streamlining their operations.
Why is warehousing management important?
Warehouse management can be a valuable aspect of business operations. We explore this in more detail below.
Inventory management
To put it simply, inventory management refers to the process of storing, ordering, and selling inventory.
Effective inventory management is an important aspect of warehouse management. It can better position you to keep track of your stock. Being out of stock or overstocked can create issues for small businesses. This could potentially lead to reduced sales, customer dissatisfaction and increased costs.
Inventory management can:
- Provide you with real-time stock levels
- Help you make sales forecasts and projections
- Enable you to track business performance
- Help stop you from overselling.
Customer experience
Successful warehouse management can also help enhance customer experience. When products are readily available, it’s easier to fulfill orders quickly. And improve delivery timeframes.
This can lead to happy customers and help encourage repeat business. Learn more about how to improve customer experience and boost customer loyalty.
Scalability
Warehousing can support you as your business changes to meet customer demand. By being strategic about your warehouse management it can help make it easier for you to scale your business.
You can also leverage economies of scale. This is the situation where, as the quantity you buy goes up, the cost per unit goes down. Warehousing can help enable you to make bulk purchases at better prices.
The elements of efficient warehousing management
There are many different elements that you’ll need to consider when it comes to warehouse management. Let’s break some of these down below.
Inbound and outbound shipment handling
How will you manage receiving stock to your warehouse? And how will you distribute goods to your customers? Learn more about how to choose a shipping cost method that suits your delivery process.
You’ll need to decide how you’re going to manage both inbound and outbound shipments.
Inbound handling can include things like:
- Sourcing and purchasing
- Recording and receipts
- Quality control
- Stock replenishment
- Tracking expected arrival of bulk shipments.
Outbound handling can include things like:
- Customer order processing
- Picking and packing orders
- Transportation of goods to customers
- Communicating updates to customers
- Returns processing.
Storage strategies
It’s important to keep your warehouse organised. This can help increase efficiency and help you maximise space.
There are many different storage strategies to help keep you organised, for example:
- Warehouse zoning
- Labelling
- Sorting in product specific containers
- Pallet stacking
- Making use of vertical space.
Storage strategies can help you arrange products in a way that minimises the time and effort required to retrieve them.
Climate control
Climate control is another important aspect of warehousing management. A controlled climate can help preserve the integrity and quality of your goods. Temperature, humidity, air quality and air flow are all important aspects of warehouse climate control.
Security
It’s important to protect the safety of your products. Consider taking adequate security measures as part of your warehouse management. This can include things like security cameras, surveillance, locks and access control.
Warehousing technology
There are many different types of warehousing technology available. These tools can provide real-time insights such as the quantity and location of each item in a warehouse.
This software can help automate processes. Plus, help reduce the need to complete manual or mundane tasks. For example, counting inventory items. This can help save time and improve accuracy.
Integrating warehouse management with eCommerce
By integrating your warehouse with your eCommerce platforms you can enjoy many benefits. We discuss how an eCommerce warehouse can help both you and your customers below.
Automated order processing integration
With automated order processing, orders placed on your eCommerce platform are automatically sent to your warehouse. This reduces the risk of errors associated with manual order entry.
Automated order processing can be an important component of your eCommerce warehouse. It can help streamline order fulfilment, without the need for manual intervention.
Automated order processing software can also help generate shipping labels. These labels can capture the chosen shipping method, delivery address and other useful information. This can help speed up the delivery process and reduce the probability of making mistakes when shipping your products.
Online returns integration
Consider facilitating an online returns process that integrates directly with your warehouse.
With the right setup in place, your warehouse and eCommerce platform can help you process returns and update inventory. A seamless returns process can help enhance customer satisfaction and help you recover stock.
Learn more about how to create a returns policy for your online business.
Customer experience integration
Integrating your eCommerce platform with your warehouse is a great way to help improve customer experience. And enable effective communication with your customers.
You can set up automated status updates to provide transparency and help build trust. This can include sending an email or SMS message to customers upon order confirmation, shipping, tracking and delivery.
Consider connecting your customer support system with your eCommerce platform and warehouse. This means you’ll be able to provide accurate responses to customer questions. And answer enquiries about orders, shipping and returns.
Learn more about how to manage your eCommerce supply chain as an online business.
Warehousing management can be a powerful tool for small businesses wanting to thrive. It can help optimise your supply chain while enhancing customer experience and business operations.
Warehouse management processes
Warehouse management typically revolves around six steps. The efficiency of each directly impacts the next. Therefore, it's important that every step goes smoothly for the overall warehouse operation. We break this down in more detail below.
- Receiving - This initial step involves checking-in and properly logging all incoming items. Here you need to verify that the right quantities have been received and they are in good condition.
- Put-away - Once received, items need to be transitioned from the receiving dock to their designated storage locations.
- Storage - How inventory is stored and arranged can play a big role in enabling fast and accurate picking. Safe storage with logical organisation is key.
- Picking - This process includes retrieving the specific items needed to fulfill orders.
- Packing - The picked items must be carefully packed using the correct materials and packaging, with an accurate packing slip included.
- Shipping - The final step is getting orders shipped out, with the correct documentation. This will help facilitate on-time delivery for customers.
Each step builds on the previous one. Optimising all six processes and minimising errors will help you achieve efficient warehouse operation.
Selecting fulfillment strategies that align with a company's size, order volume and order types is another thing you should consider. This can yield significant benefits, including faster product shipping, reduced waste and improved customer satisfaction. Tailoring picking strategies to the kinds of orders received is important for workflow efficiency. We unpack this in more detail below.
Warehouse management picking strategies
- Batch picking - This technique enables quickly fulfilling multiple orders for the same product by eliminating redundant trips to that inventory location.
- Zone picking - Pickers are assigned specific zones or areas.
- First expired, first out (FEFO) picking – This method prioritises shipping products with sooner expiry dates first.
- First in, first out (FIFO) picking - The first products received into your inventory are the first ones picked and distributed. This helps prevent your older stock from becoming obsolete.
Implementing tech
Technology also plays an integral role in optimising fulfillment strategies. Handheld mobile devices displaying packing lists, item locations, serial numbers and lot data can significantly enhance picking speed and accuracy.
The right combination of fulfillment strategies and enabling technologies can dramatically improve your warehousing capabilities.
Choosing a warehouse management system
Picking the right warehouse management system (WMS) depends on the specific needs of your warehousing operation. Above all, the WMS you choose should help boost efficiency and order accuracy. A great WMS does more than just increase productivity. It acts as a guide, helping all warehouse staff make the most of their time. How? By providing real-time insights into every part of operations - receiving, shipping, inventory, order fulfillment, labour and more. Having these insights allows both managers and workers to identify areas for improvement.
With the right WMS in place, your entire warehouse operation can level up. It can help with greater efficiency and pinpoint order accuracy.
Warehousing management can be a powerful tool for small businesses wanting to thrive. It can help optimise your supply chain while enhancing customer experience and business operations.
Originally published November 2023, updated August 2024.
Help customers find your business online
With online marketing solutions designed to help direct customers to your business website.
Explore more on this topic
Insights to power your business today and tomorrow
Download your Tech State of Play report to help propel your business further through technology.